On 7 January, CFDA released the Regulations
on Record of Food Safety Traceable Information of Infant Formula Production
Enterprises. The policies targeted at product safety will push companies to build
vertically integrated operations where possible.
Product safety is clearly critical to the
development of the infant formula industry. In a move designed to build up
consumers’ confidence and ensure whole-process traceability of infant formula
production, the China Food and Drug Administration (CFDA) released the
Regulations on Record of Food Safety Traceable Information of Infant Formula
Production Enterprises (Regulations) on 7 January.
Under its terms infant formula
manufacturers are required to provide full production information, and
establish and improve their food safety traceability systems, whilst their
responsibilities are highlighted.
The Regulations make it clear that infant
formula producers must code the batch number uniquely based on production date,
and file the codes as production records and as a basis for their food safety
traceability system, retaining these records for at least 3 years.
Manufacturers are required to accurately record the personnel in charge of
production planning and direction and key indices such as production quantity,
the plant’s environmental records (temperature, humidity, etc.),
cleaning/hygiene maintenance records, raw materials, operating times/operators
etc. to ensure the traceability through every stage of the process.
Regarding sales records,the Regulations
require that sales through online stores must be recorded alongside those
through traditional retail channels.
Trade sources view the traceability systems
positively:
Consumers can directly check on the
regulated production process, which should help build confidence in domestic
products
Problems and those responsible can be
identified in the event of any food safety accidents
Manufacturers will be compelled to regulate
their production, bringing quality improvement as a result
The Food Safety Law and the General
Standard for the Labelling of Prepackaged Foods for Special Dietary Uses
implemented in 2015; and the Regulations on the Administration of Formula
Registration for Infant Formula which is likely to be issued this year, along
with the Regulations, are being referred to as the “strictest ever policies” by
domestic media. Certainly they were already impacting the industry in H2 2015,
even though some had not yet been issued.
Some dairy companies, in order to deal with
the regulation on labelling, lowered their prices on the products with outdated
labelling. (Note: the new rules required packs of imported infant formula to be
labelled in Chinese, without which they would be returned or destroyed, whilst
for domestic products, Stage 1 formula labels were no longer permitted to
highlight typical and widely used ingredients – for example, DHA or whey
protein – and make a feature of how high their content is, or mislead consumers
by claiming curative capabilities for a product.)
“In the situation where
enterprises are busy adjusting product categories and running down their
inventories, the whole infant formula industry is seeing declines in profit.
However, sales promotion is not a long-term strategy”, said industry
commentator Wang Dingmian.
In particular, full control of the supply
chain is increasingly the target of the leading local formula producers.
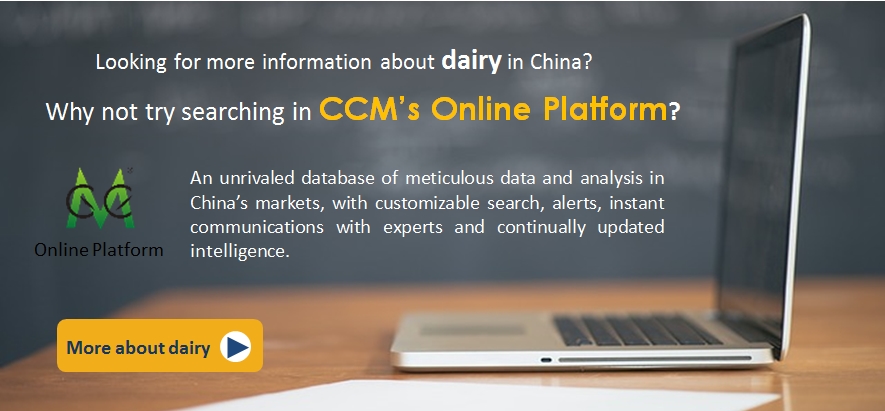
Bright Dairy and Feihe Dairy respond to
“the strictest ever policies”
On 29 December, 2015, Bright Dairy and Food
Co., Ltd. (Bright Dairy) released the first Food Safety White Paper in China,
indicating that this was a direct response to the new Food Safety Law. It
summarised the measures it has taken already:
In recent years, it has been shutting down
minor and dispersed dairy plants and investing in large-scale dairy farms. Now
it claims its milk is 100% sourced from “largescale, quality and healthy” dairy
farms.
It has drawn up lists of 32 key measures
for supervising and controlling 55 specific risks in its dairy farms. By the
end of 2015, it owned 35 largescale dairy farms (according to the Ministry of
Agriculture, >300 cows), with a total of 80,000 cows.
It recognises 79 points of risk during the whole production process.
Additionally it has invested strongly in technology: production is carried out
in fully enclosed pipelines, with all products checked/monitored at between 808
and 1,581 separate points in the production line
Zhang Chongjian, President of Bright Dairy
said: “Under the new circumstances, an integrated supply chain is the key to
ensuring the quality of dairy products. Now we are basing our core
competitiveness on our safety control system”.
Heilongjiang Feihe Dairy Co., Ltd. takes a
similar stance, in line with its traditional business proposition: “There are 2
critical links: one is the upstream production, the other is the marketing.
Producing our own milk is vital”. Feihe Dairy believes it has now achieved
whole process traceability and control, from forage grass planting, largescale
dairy farming, production and processing, logistics and storage through to
channel supervision and control and even to after-sale service.
This article comes from Dairy Products China News 1601, CCM
About CCM:
CCM is the leading market
intelligence provider for China’s agriculture, chemicals, food &
ingredients and life science markets. Founded in 2001, CCM offers a range of
data and content solutions, from price and trade data to industry newsletters
and customized market research reports. Our clients include Monsanto, DuPont,
Shell, Bayer, and Syngenta. CCM is a brand of Kcomber Inc.
For more
information about CCM, please visit www.cnchemicals.com or get in touch with us directly by emailing econtact@cnchemicals.com or calling +86-20-37616606.
Tag: Infant Formula dairy